What does it take to bring cotton from the farm to your closet? Following conventional standards, the multi-step process typically includes heavy pesticide applications, thousands of liters of water, and often, labor abuses.
Conventional cotton production is characterized by high rates of insecticide use relative to other crops, and in some regions it continues to be scrutinized for forced and child labor.
To address these challenges, a coalition of major global brands came together in 2005 under the leadership of the World Wildlife Fund to create a set of global sustainability standards for cotton farmers. Four years later, the organization published the Better Cotton Standard System that provided a singular global definition of “Better Cotton.”
The Better Cotton Criteria focus on six key principles: crop protection, water, soil health, biodiversity, fiber quality and decent work. The Better Cotton Initiative (BCI) is now the largest cotton sustainability program in the world.
“Cotton affects so many livelihoods around the world,” said BCI’s U.S. Country Manager Scott Exo. “Any incremental improvements to human health and economic welfare can end up making a positive impact for a lot of people.”
In 2017, program partners trained 1.6 million farmers from 23 countries, and BCI farmers produced 2.5 million tons of cotton during the 2015–2016 season. Currently, Better Cotton makes up 12 percent of total global production.
The results thus far have been positive. “When comparing BCI member farms in India to nonmember farms in the same area, we saw a nine percent increase in crop yield, a 20 percent decrease in pesticide use, a 20 percent reduction in water use, and a 23 percent increase in profit,” said Exo. “We’ve seen similar comparative outcomes in China, Pakistan, Turkey, Senegal and more.”
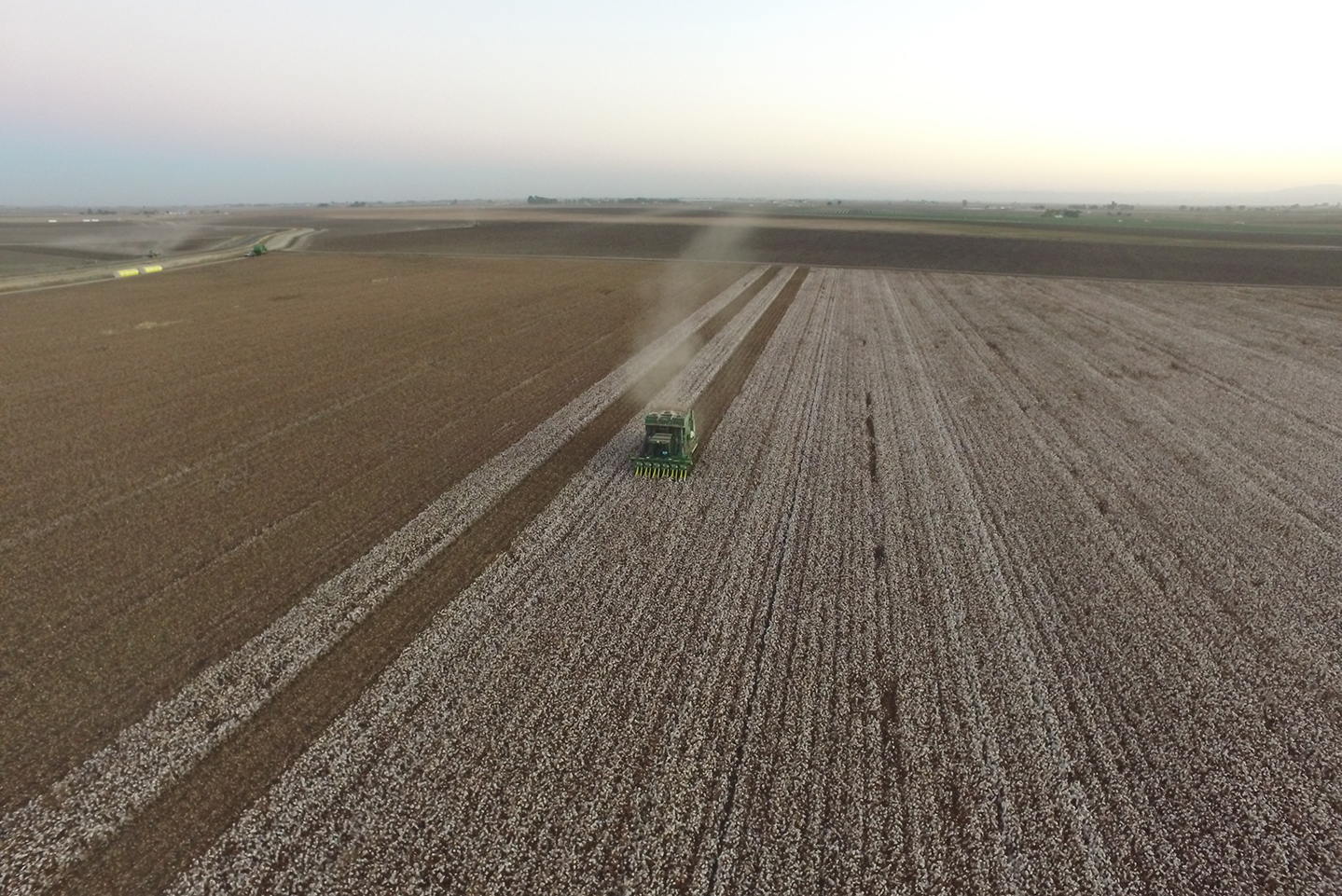
Improving farmers’ livelihoods
BCI, committed to reducing environmental impacts and improving production over the long term, coordinates a capacity building program to help farmers around the world adopt Better Cotton production principles. Member retailers and brands contribute to a fund that provides grants to implementing partners to train farmers at the field level. This dual-track business model — with BCI managing standards credibility and growth and implementing partners focused on ground-level leadership — is a cornerstone of BCI’s program.
“The built-in capacity building model is the thing that is really unique about BCI,” said Exo. “In addition, while smaller certification programs have struggled with revenue models, the BCI Secretariat [the standard holder] is largely self-funded through membership fees from brands, retailers and suppliers. We don’t have to struggle to operate from grant to grant.”
Member partners see intrinsic value in participation as well.
“This whole BCI thing is really something I believe in,” said Quarterway Cotton Growers General Manager and BCI implementing partner Todd Straley. “Sustainability is the direction we are headed. Farmers are going to have to do a better job of marketing themselves and the products they produce to millennial consumers. BCI helps us with that.”
Straley’s gin processes cotton from a group of about 50 cotton farmers in West Texas. He works with each farmer to ensure they are meeting BCI standards and reporting on them annually.
“For the most part, a U.S. cotton grower is already doing everything that BCI requires,” said Straley. “The benefit with BCI is that it makes the farmers pay more attention because there is more documentation involved. They are putting their notes into a formal assessment, and that process helps to reinforce the impact of their practices.”
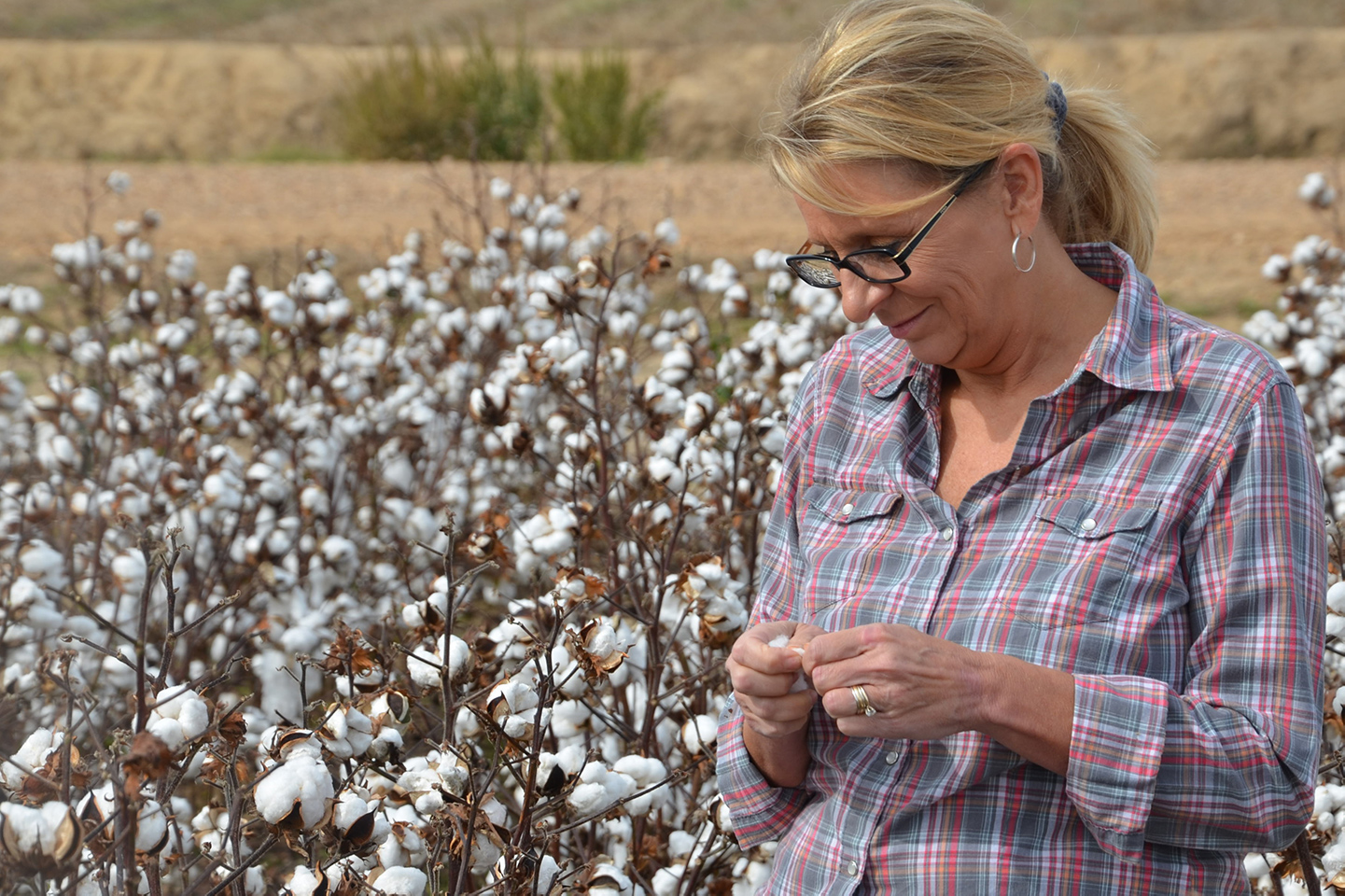
Verifying global compliance
To verify member farms’ compliance with BCI’s minimum criteria and performance against improvement indicators, the organization uses a combination of self-assessments, second-party credibility checks and third-party verification.
To be licensed to grow Better Cotton, farmers must meet minimum requirements set forth by BCI. To incentivize farmers to continue to improve, BCI grades them based on their improvement indicator scores. Those with the highest scores receive longer Better Cotton licensing periods.
The assurance system categorizes farms by size — smallholders, medium and large — to accommodate differences in needs and scale. For example, BCI standards allow an exception for family smallholders to have their children work on their farm so long as it does not pose risks to their health, safety or development.
“BCI’s decent work criteria, including child and forced labor, are very extensive and grounded in international labor convention standards,” said Exo. “These standards are more detailed for the large farm context because the risks for labor exploitation and other exposure to dangerous situations is greater where there are more employees.”
From the farm to the clothing store, traceability gets more complicated.
After it is picked, cotton is shipped for processing to various facilities, starting in the gin to separate the fibers from the seeds and pods. The bales of raw cotton fibers are then sold to merchants, who distribute the bales to yarn production facilities. At this point, lint from several bales is blended to produce more uniform fiber properties. This helps expedite the automated spinning process.
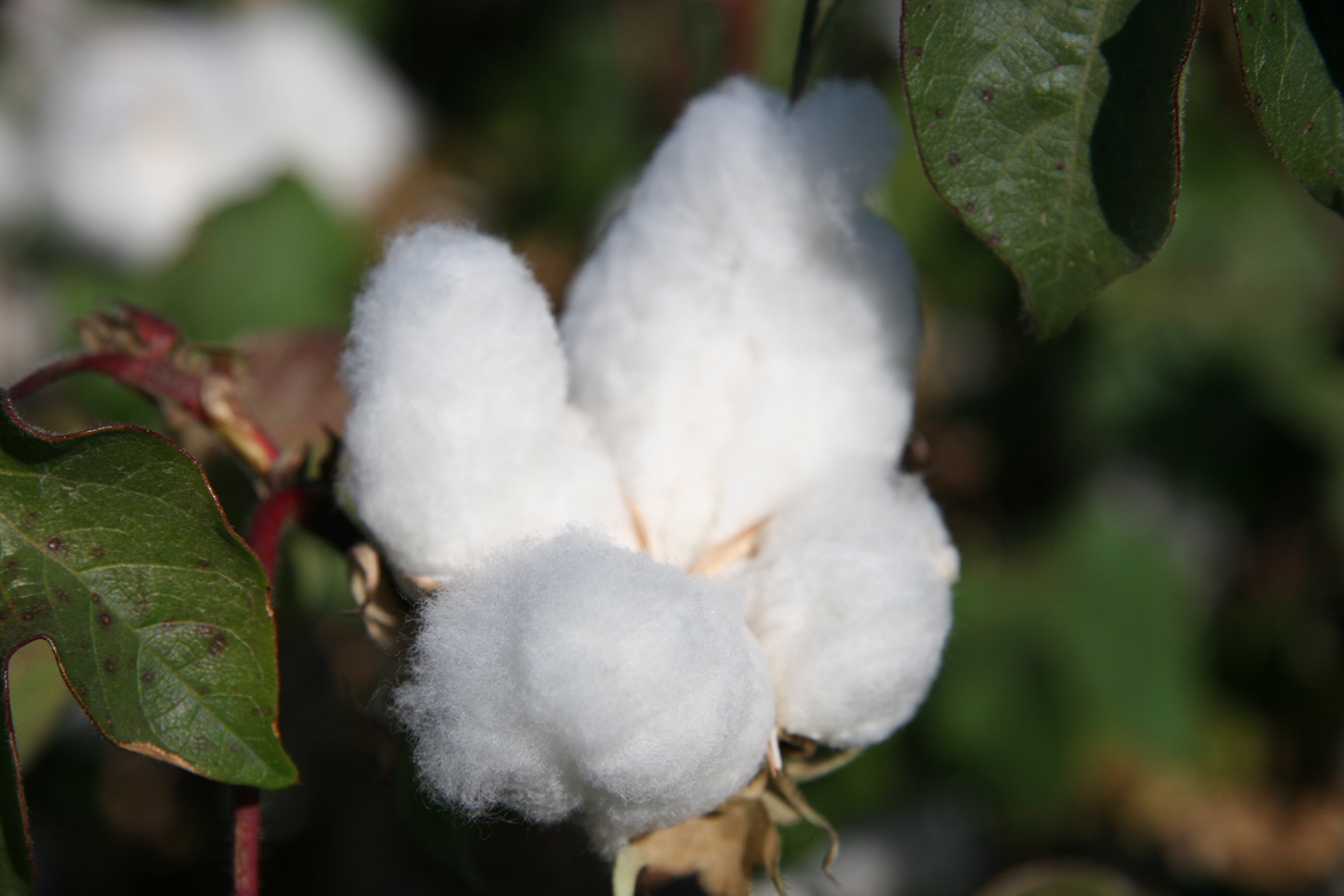
The spools then make their way into commercial textile plants, where they are woven into fabrics. These fabrics are then shipped to clothing producers for finishing into garments.
With cotton’s long and complex global supply chain, BCI employs a Chain of Custody system to measure implementation.
From participating farmers to the gin, Better Cotton is segregated from conventional cotton. After the gin, an online MassBalance system allows traders to mix or replace Better Cotton with conventional cotton from the same country, and for spinners to mix or replace Better Cotton with conventional cotton from any country. Because Better Cotton is not necessarily used in a retailer’s BCI order, they may receive a credit called a Better Cotton Claim Unit (BCCU) that accounts for one kilogram of Better Cotton in the overall supply chain. In this way, retailers can claim BCCUs in support of more sustainable cotton production under BCI standards without disrupting their ability to source cotton of any quality when they need it. In addition, end consumers who purchase products with BCI labels don’t end up paying much more than they would for products that don’t include BCI labels.
“The Mass Balance system is how we account for the good that is being created by farmers meeting the requirements of BCI licensing,” said Exo. “Our model works in the same way that green tags work in the renewable energy industry. As a consumer, I can pay a little extra on my bill to support renewable power. The utility company, in turn, accounts for all the renewable units purchased, and the electricity in my home may actually be coming from a coal plant in Montana.”
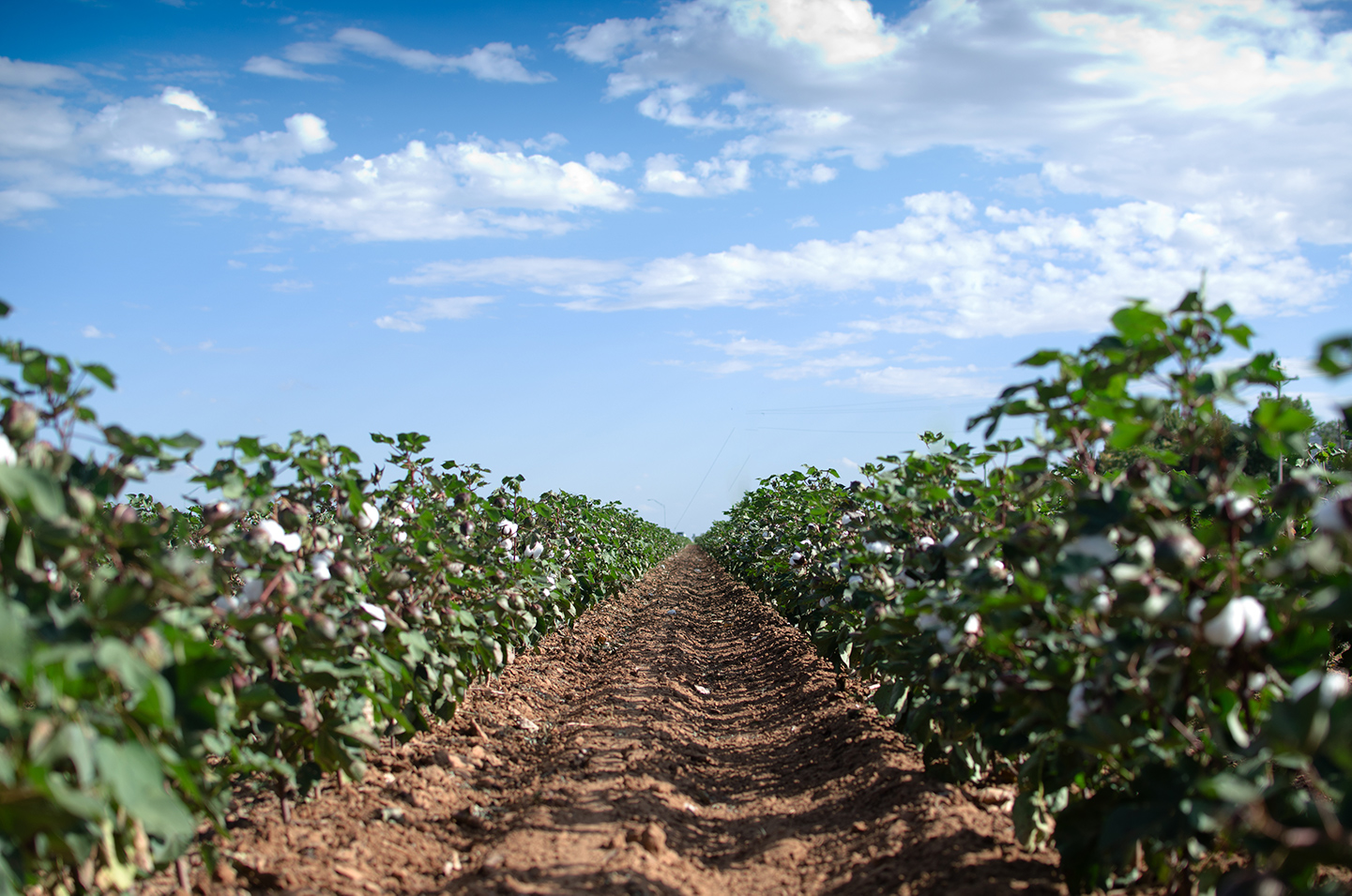
Going beyond BCI to full system transparency
Since BCI standards apply to production only, larger retailers and brands concerned about sustainability and labor issues throughout the entire supply chain may require manufacturers and mills to comply with Worldwide Responsible Accredited Production (WRAP) standards. WRAP certifies safe, legal, socially responsible and ethical manufacturing practices around the world.
For a smaller group of cotton growers, suppliers and retailers, when third-party standards alone didn’t meet their needs, they teamed up to take traceability into their own hands. Together they created PimaCott.
Until recently, pima cotton, a premium extra-long staple variety grown primarily in California, was not being traced at every step in the production process, so products labeled as pure pima could contain anywhere from 20 to 80 percent pima cotton. Then in 2014, Bowles Farming Company President Cannon Michael was approached by a major retailer that had run some tests on sheets labeled as pure pima cotton and found that they weren’t pure pima after all.
“The results of their tests were really staggering to see, with more than 80 percent of products containing either a blend of cottons or no pima at all,” said Michael. “The issue is that consumers think they are paying more for a premium product. But in truth, the suppliers are mixing cotton to reduce their costs and still selling the product for a premium price.”
To address the purity issue, a group of California pima cotton farmers, including Michael, joined forces with a textile company, an agricultural merchant and a research lab to develop a specialized DNA marker that can be applied to pima cotton during the ginning process. The marker allows for tracking at every step in the process, all the way from the farm to the consumer.
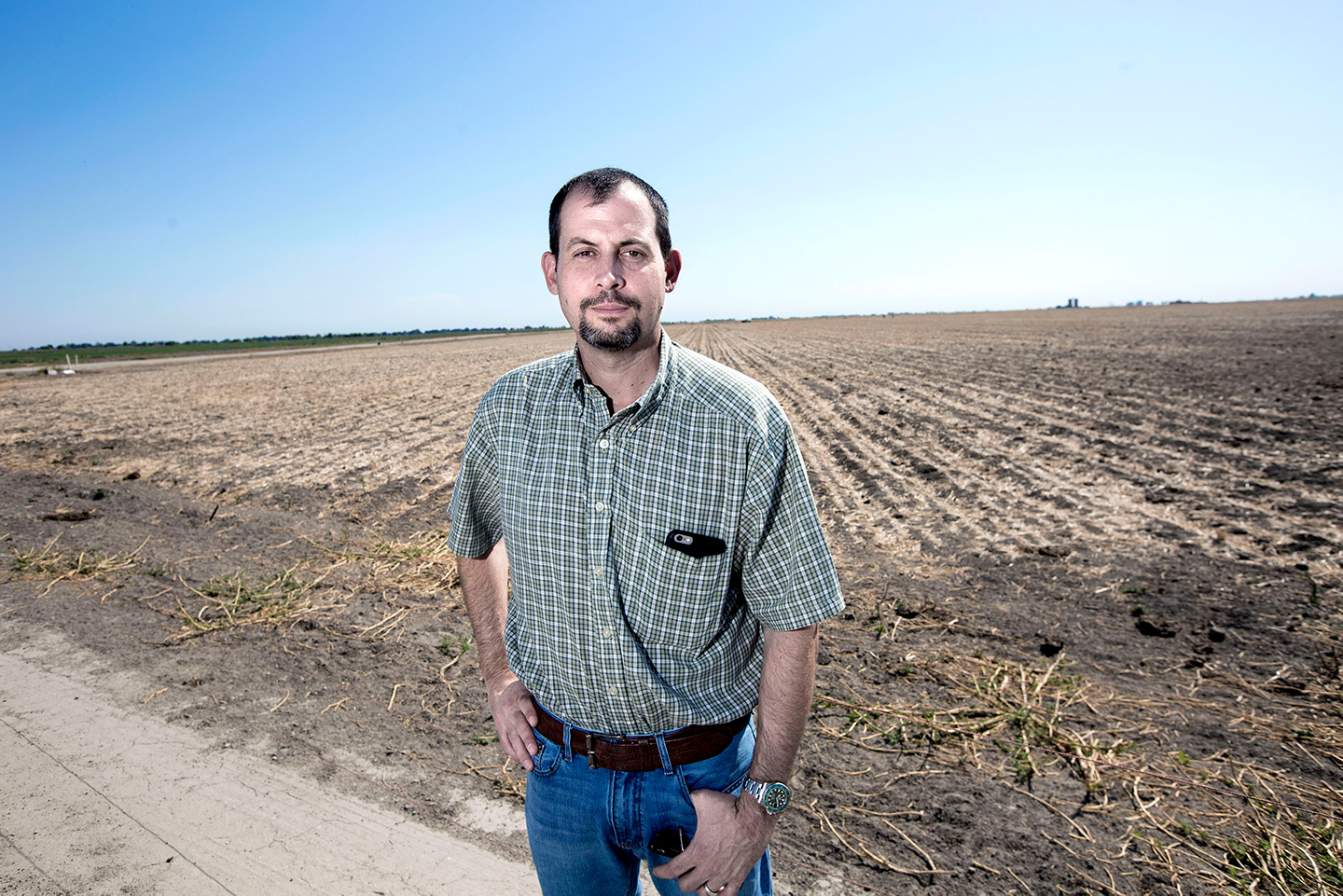
anything. It does cost more, but there’s also a story behind it.” – Cannon MichaelPhoto courtesy of Bowles Farming Co.
Michael’s gin was the first to be modified with the DNA tracing technology, and their merchant followed suit by purchasing the DNA tagging mechanism. They now work exclusively with a mill in India that installed a state-of-the-art facility following specific PimaCott protocols. Working together, they were able to create a pure product that consumers can trust.
For Michael, the upfront costs were worth it, as long-term business investments and to ensure product integrity.
“Without traceability, you can’t really have true sustainability,” he said. “We need to move away from the thought process that sustainability doesn’t cost anything. It does cost more, but there’s also a story behind it. I sleep on sheets now that I know came from our gin and a handful of family farmers in California. And I’m proud to support them. I’d rather a customer with five T-shirts in their closet that they know weren’t produced with slave labor than a whole wardrobe of clothing from who knows where.”
Articulating it for consumers
Traceability in sustainable cotton production takes many forms.
Currently, a BCI label denotes that the clothing or linen brand has purchased enough BCI credits that they are a supporter of BCI sustainability standards. It does not mean that the garment itself contains sustainably grown cotton. Alternatively, PimaCott labeled products are guaranteed to contain 100 percent pure pima cotton. Other certification programs like the Global Organic Textile Standard oversee adherence to organic standards throughout the supply chain and provide options for consumers looking to wear organic or sustainably produced attire.